SDNL550 SDNL600 SDNL650 SDNL700 SDNL750 SDNL800 SDNL850 SDNL900 SDNL950 SDNL1000 SDNL1050 SDNL1100 SDNL1150 SDNL1200
SDVL550 SDVL600 SDVL650 SDVL700 SDVL750 SDVL800 SDVL850 SDVL900 SDVL950 SDVL1000 SDVL1050 SDVL1100 SDVL1150 SDVL1200
SVNL550 SVNL600 SVNL650 SVNL700 SVNL750 SVNL800 SVNL850 SVNL900 SVNL950 SVNL1000 SVNL1050 SVNL1100 SVNL1150 SVNL1200
SVVL550 SVVL600 SVVL650 SVVL700 SVVL750 SVVL800 SVVL850 SVVL900 SVVL950 SVVL1000 SVVL1050 SVVL1100 SVVL1150 SVVL1200
SFNL550 SFNL600 SFNL650 SFNL700 SFNL750 SFNL800 SFNL850 SFNL900 SFNL950 SFNL1000 SFNL1050 SFNL1100 SFNL1150 SFNL1200
SFVL550 SFVL600 SFVL650 SFVL700 SFVL750 SFVL800 SFVL850 SFVL900 SFVL950 SFVL1000 SFVL1050 SFVL1100 SFVL1150 SFVL1200
Ratio: 18 20 22.4 25 28 31.5 35.5 40 45 50 56 63 71 80 90 100 112 125 140 160 180 200 224 250 280 315 355 400 450 500 560 630 710 800
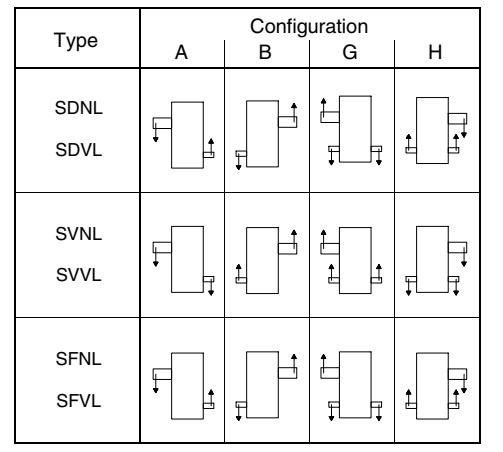
The gear units are characterised by a low noise level, which is achieved by helical gears with a high contact
ratio and a sound¬damping housing.
The good temperature characteristics of the gear unit are achieved by its high degree of efficiency, large
housing surface and performance¬related cooling system.
A number of shaft configurations (types and rotation directions) are possible. These are shown in the
following table as solid shafts: The arrows with the direction of rotation show the correlation between the
directions of rotation of the input and output shafts.
The helical¬gear teeth are case¬hardened and ground. The high quality of the teeth leads to a significant
noise reduction and ensures safe and reliable running.
Load sharing ensures that the input power introduced is shared out between two lines and transmitted to
the gear of the output shaft via the pinions of both lines. This results in dual use of the larger gear of the
output stage and permits its design using smaller dimensions.
The gears are connected with the shafts by interference fits and parallel keys or by shrink fits. These types
of joints transmit with adequate reliability the torques generated.
Lubrication of all geared parts and of the bearings is effected by a combined splash and forced lubrication
via a motor¬driven pump.
Depending on requirements, radial shaft¬sealing rings, or Taconite or Tacolab seals are mounted at the
shaft exits to prevent oil from leaking from the housing and dirt from entering it.
Radial shaft¬sealing rings
Radial shaft¬sealing rings are the standard type of seal. They are fitted preferably with an additional dust
lip to protect the actual sealing lip from external contamination.
Taconite seal
Taconite seals were specially developed for use in a dusty environment. The penetration of dust is
prevented by a combination of three seal elements (radial shaft¬sealing ring, lamellar seal and
grease¬charged re¬chargeable labyrinth seal)
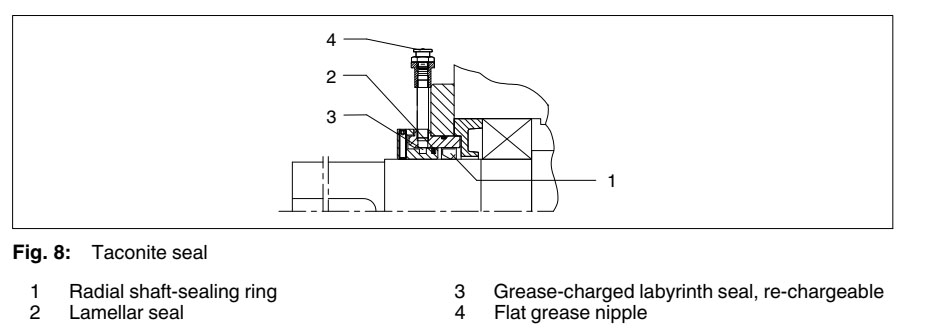
Tacolab seal
Tacolab seals are non¬contacting seals, operating wearfreely and requiring very little maintenance and
which thus ensure favourable temperature characteristics. They can be used only with additional forced
lubrication of all bearings and with reduced oil level.
The Tacolab seal is made up of two parts:
─ an oil labyrinth preventing lubricating oil from escaping
─ dust seal filled with grease, which permits the use in very dusty environments.
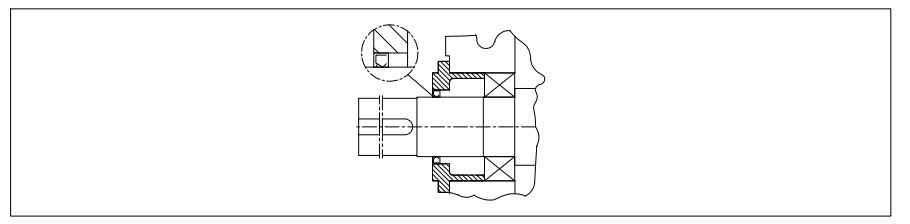
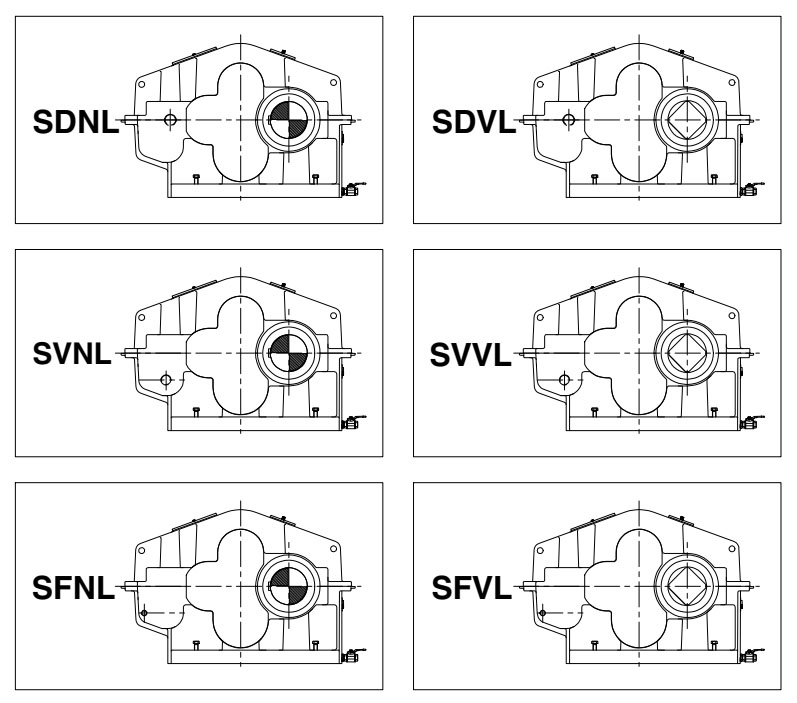